"There is a great satisfaction in building good tools for other people to use."
(Freeman Dyson)
Many people regard the lathe as the forerunner of modern machine tools. Its introduction that made turning operations possible, marked the dawn of machining. Today, turning is still one of the most commonly used machining processes, and lathes remain a substantial part of the global machine tool inventory. This is why turning tools make up a considerable portion of the product range for leading cutting tool manufacturers.
It is not surprising that LOGIQUICK, ISCAR's latest campaign, brings new developments to the market with a significant focus on innovation in the field of turning tools. Some of the newly introduced products extend the existing families within ISCAR's turning line, while others offer unique solutions for advanced manufacturing. Such novelties not only reflect the trends of modern metal cutting but also aim to enhance the profitability of machining operations, particularly in turning.
Several key features characterize the development directions in turning tools, including the following:
- Higher Efficiency and Precision: This involves turning tools that can enhance productivity and precision, accelerate the overall machining process, and minimize waste.
- Advanced Cutting Materials and Progressive Coating Methods: Cutting-edge materials such as ceramics and cubic boron nitride (CBN) are becoming more common in turning tools. Due to excellent heat resistance and durability, these extra-hard materials offer superior cutting speed when compared to traditional tungsten carbide. Concurrently, the need for rapid metal removal is driving interest in progressive coating technologies for cemented carbides. Innovative coatings can enhance cutting capabilities, extend tool life, and reduce wear.
- Multi-Directional Turning Tools: These high-quality, versatile tools not only increase productivity and machining efficiency by reducing the number of tool changes but also minimize tool inventory, decrease machine downtime, and maintain tighter tolerances.
- Digitalization: The Industry 4.0 approach underscores the importance of a turning tool's digital component as an integral part of smart manufacturing.
- Sustainability: Given the pressing nature of environmental issues, there is a growing demand for cutting tools, including turning tools, which have a smaller environmental impact. This means they should be less energy-intensive and generate less waste.
With the above in mind, we should examine the new products in ISCAR's turning tool line that are part of the LOGIQUICK campaign. Indeed, turning encompasses many external and internal machining applications, including longitudinal turning, facing, profiling, chamfering, grooving, parting, and boring. Let's study ISCAR's most recent turning advancements and highlight their features.
Advanced Cutting Material to Boost Turning Efficiency ISCAR has significantly broadened the range of available ceramic grades for ISO-standard turning inserts. The recent additions to the range have been designed to facilitate efficient machining of difficult-to-cut materials, particularly hard steel and cast iron (ISO H group of application). The newly introduced carbide grade, IC1017, was specifically developed for machining challenging nickel-based superalloys. This complementary grade features a high-hardness submicron substrate and a PVD coating to enable turning superalloys at higher speeds. For cutting non-ferrous materials such as aluminum, copper, platinum, bronze, brass, and others (ISO N group of application), the product range has been enhanced with new turning and grooving inserts featuring a nanocomposite diamond-like coating (DLC).
Multi-Directional Benefits QUICK-T-LOCK is an innovative tool family designed for productive multi-directional cutting. This includes front and back turning, profiling, and facing operations, all achievable with just one tool. The family uses a unique insert-clamping concept to provide exceptional stability during machining at extremely high feed rates. A notable feature is the advanced chipformer, specially designed for high-feed turning, especially in backworking machining (Fig. 1). V-shape CUT-V-GRIP inserts offer a versatile solution for bi-directional external turning operations. The inserts, suitable for installation on modified existing holders, are capable of entering narrow machining areas where common V-type ISO inserts cannot be used (Fig.2).
Not Boring News in The Boring Line When boring with a high overhang (usually more than five bore diameters), vibrations are a common issue. These vibrations can affect surface finish, reduce tool life, increase power consumption, and limit performance. While changing cutting conditions is a typical method to reduce vibrations, it may not always be the best solution, as it can result in longer machining time. However, a new anti-vibration holder with an active vibration-damping mechanism offers an alternative approach to overcome this challenge, enabling a high level of productivity in various boring operations, from rough to finish. ISCAR's PICCO is a tool system primarily designed for machining small-sized parts. This versatile system, which can be applied to a wide range of turning, boring, threading, and drilling operations, is highly popular in workshops that manufacture various miniature components. A typical PICCO tool consists of a holder and a solid carbide cutting insert secured within the holder. The system has now evolved with the introduction of PICCO-INDEX, a family of steel and carbide boring bars designed to be mounted on existing toolholders. The bars are specially engineered to carry small ISO-standard indexable inserts (Fig. 3). The new addition offers a viable cost-effective alternative, particularly for rough and semi-finish operations for compact part production.
Swiss-Type in Focus CNC Swiss-type lathes play a crucial role in modern manufacturing due to their precision, efficiency, and ability to perform multiple operations simultaneously, such as drilling, milling, turning, and knurling. They are instrumental in the production of miniature components required in several industries, for example, watchmaking, medical devices, automation equipment, and electronics. Consequently, the development of more advanced cutting tools and toolholders dedicated to Swiss-Type lathes is a top priority for most tool manufacturers, including ISCAR. The LOGIQUICK campaign has also highlighted Swiss-Type machining tools. The new modular system, QUICKSWISS, provides a solution for most applications on the sub-spindle of Swiss-Type lathes. This system (Fig. 4), which features a height adjustment option, offers a wide variety of bases, holders, and heads for various turning operations.
For grooving, parting, and recessing, the QUICK-2-CUT family shows promise. The tools in this family carry high-precision, narrow, double-sided inserts which are tangentially mounted on the tool from the side. The insert clamping concept ensures high rigidity and excellent dimensional repeatability. The targeted coolant, directed to the cutting zone, improves tool life and contributes to a better surface finish (Fig. 5). The LOGIQ-4-TURN family of turning tools with indexable double-sided inserts has been well-received in the market. In response to this positive feedback, the company has expanded the family range to include smaller-sized inserts, providing a cost-effective solution for Swiss-Type and compact lathes. In ISCAR's electronic catalog, two new filter search options specifically related to Swiss-Type lathes have been added. These options allow for the search of modular adaptations to find more efficient tools for main and back tool posts.
***The LOGIQUICK campaign's turning package encompasses far more than the products currently under consideration. The company is gradually introducing new product families in quick succession and plans to allocate more time to analyzing these new arrivals. Will they boost productivity and contribute to a rapid increase in customer profitability? ISCAR firmly believes the answer is a resounding "yes", with an added message to the manufacturer: "Be quick to follow up on new advantages in turning operations!"
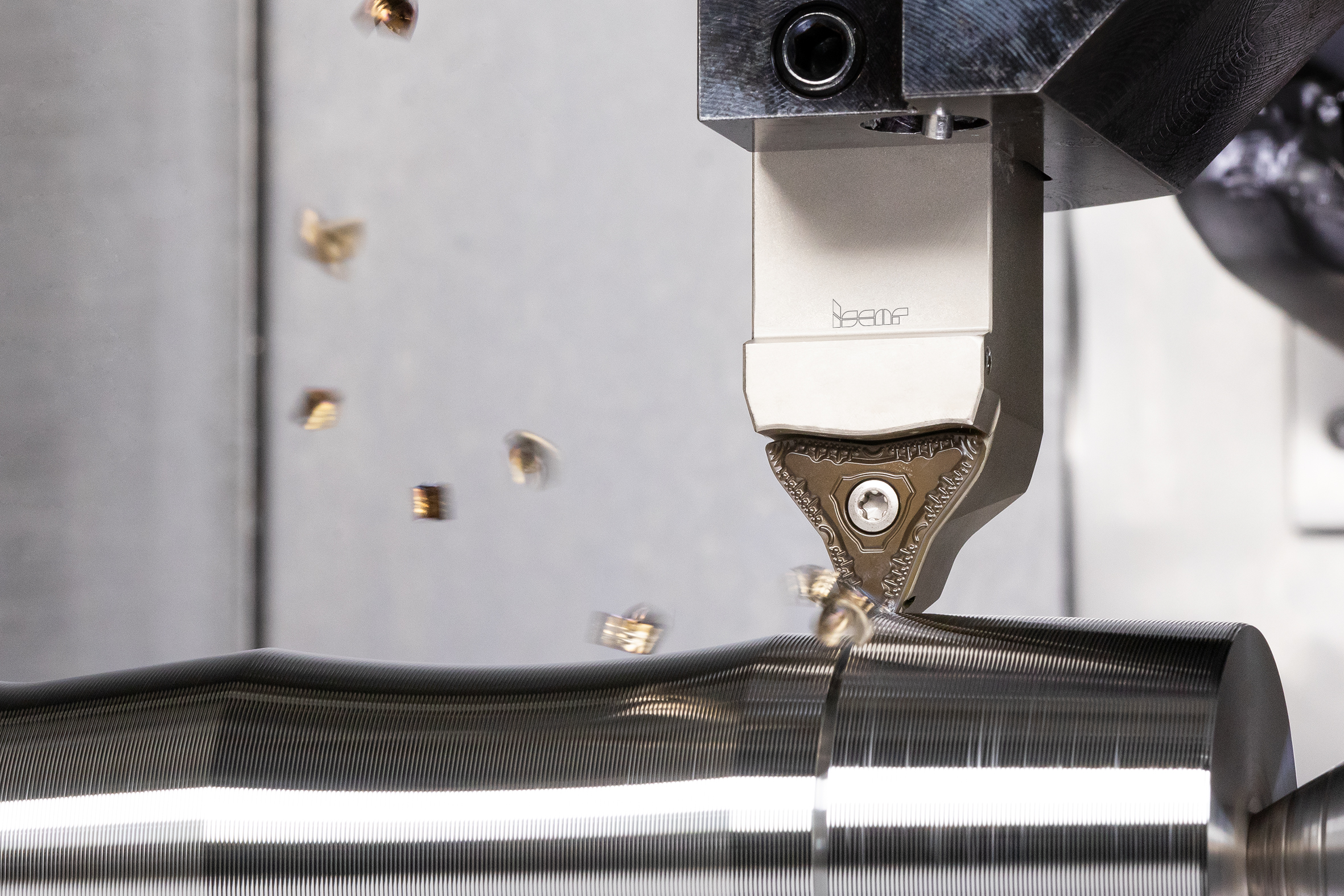
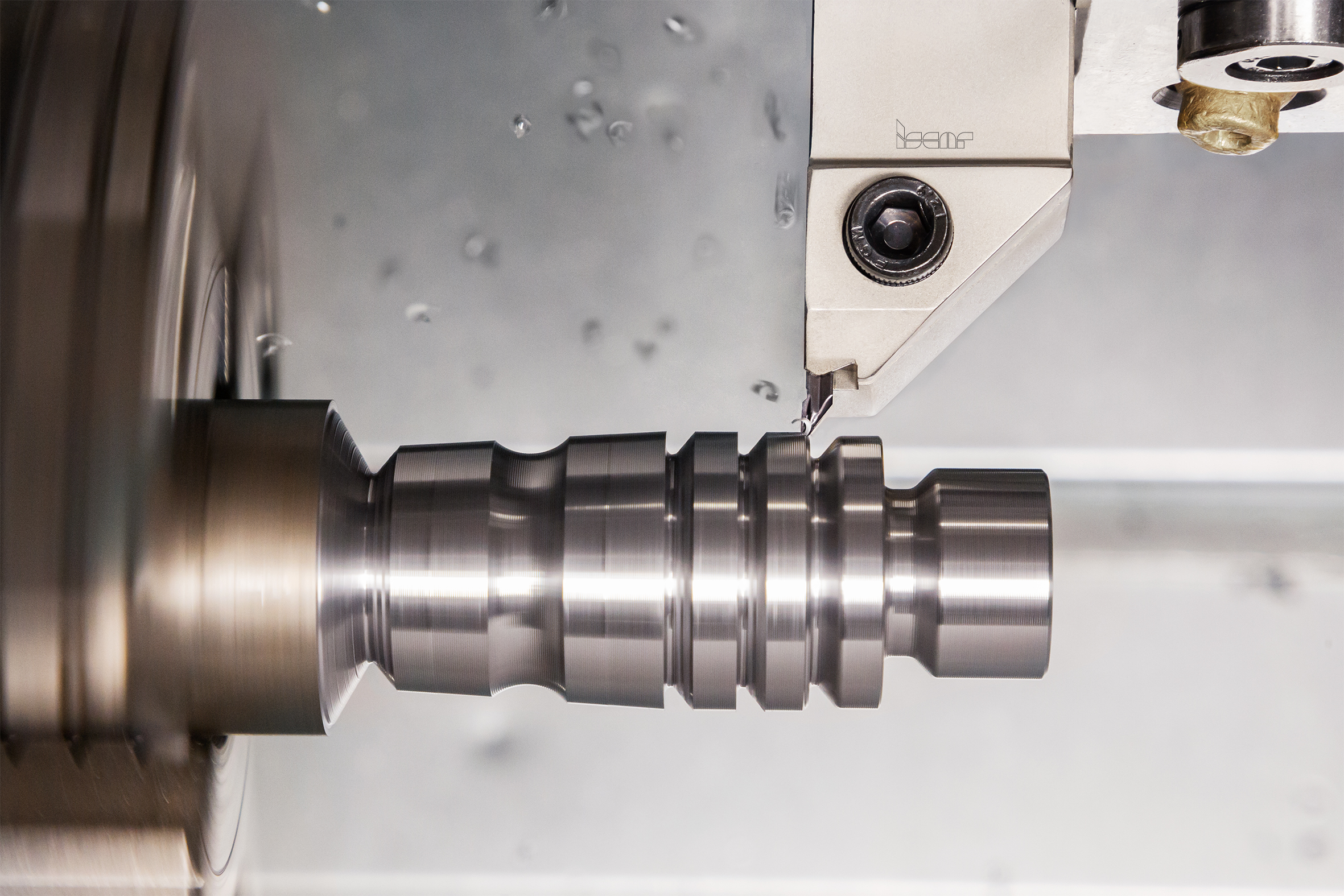
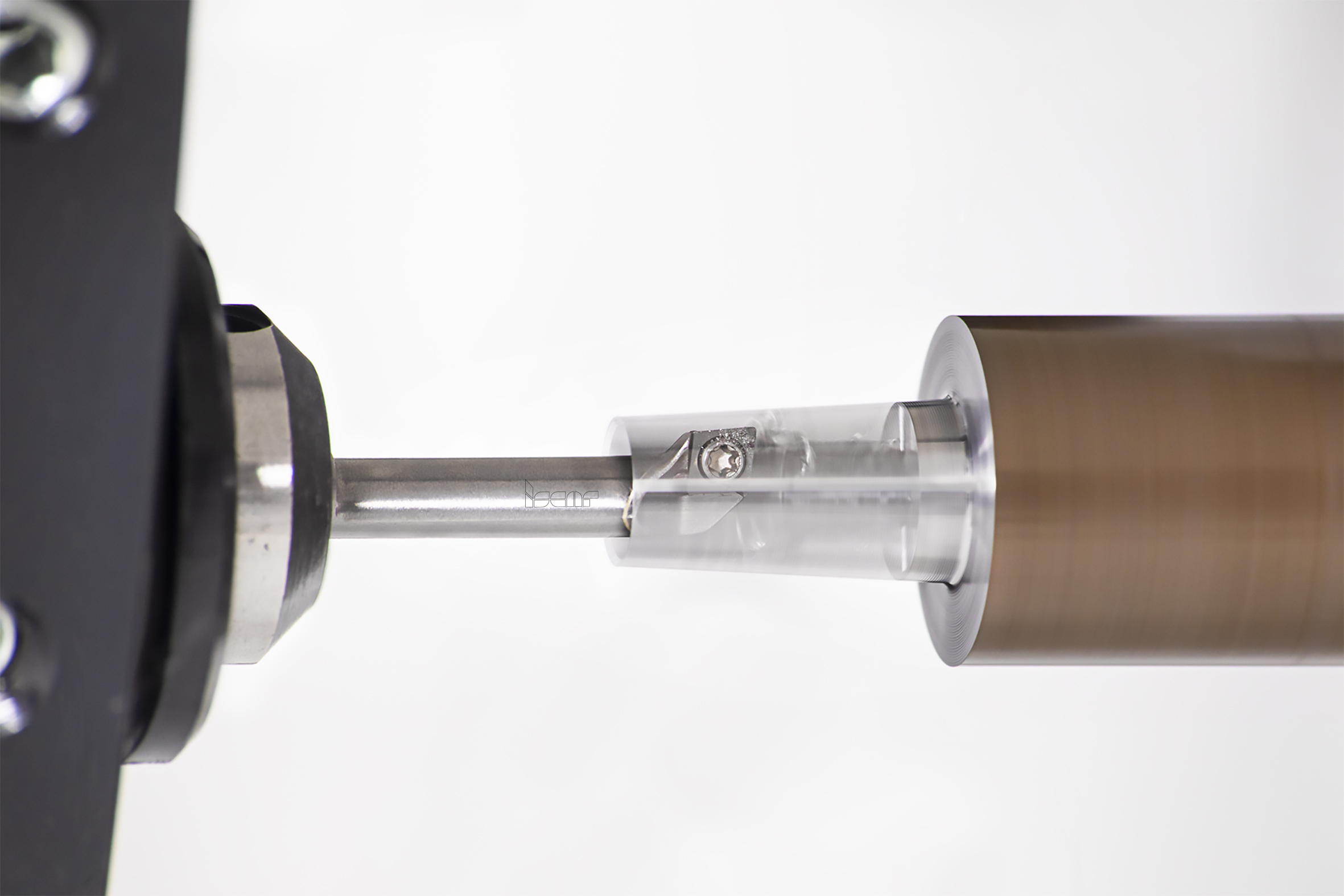
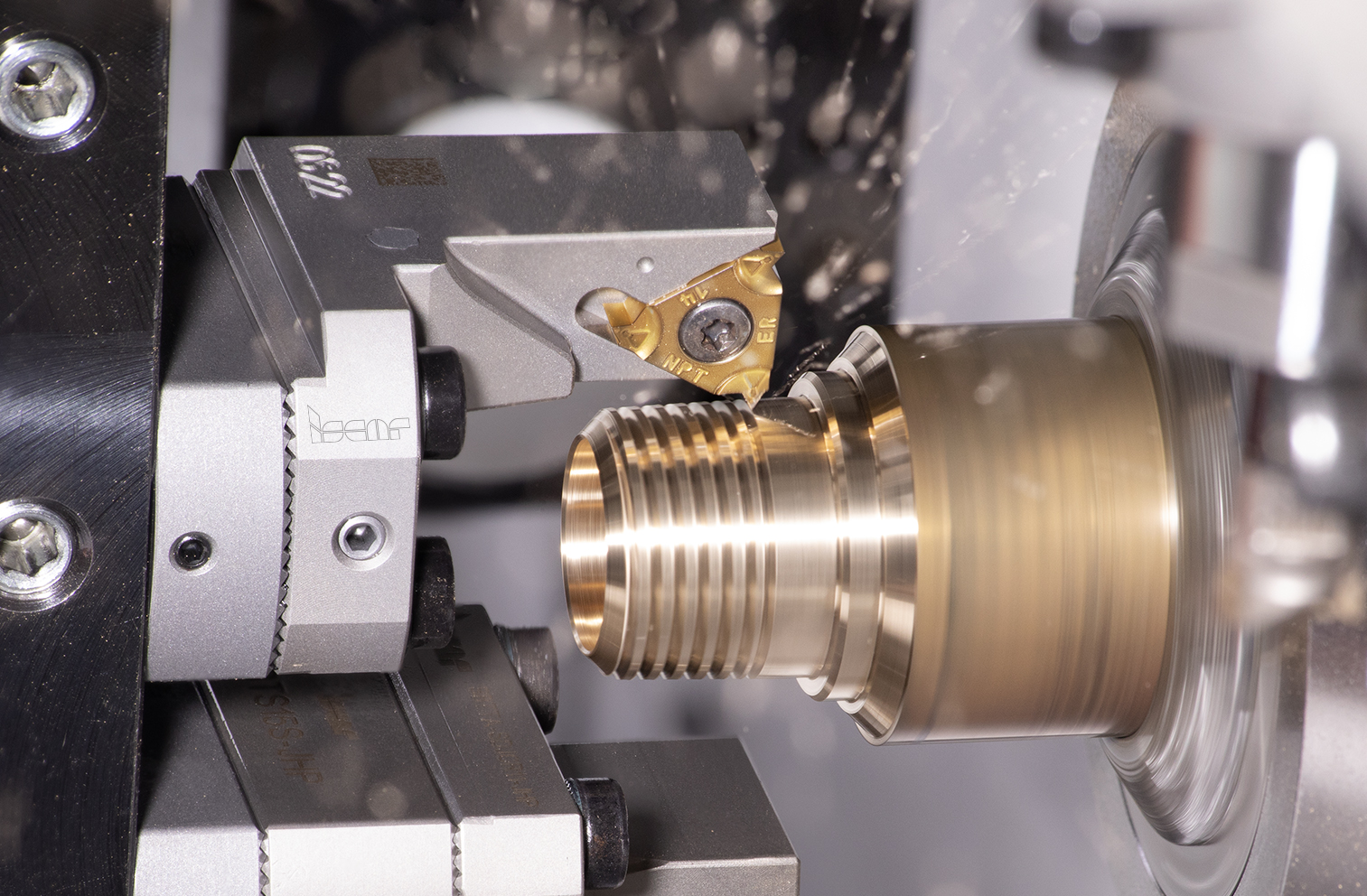
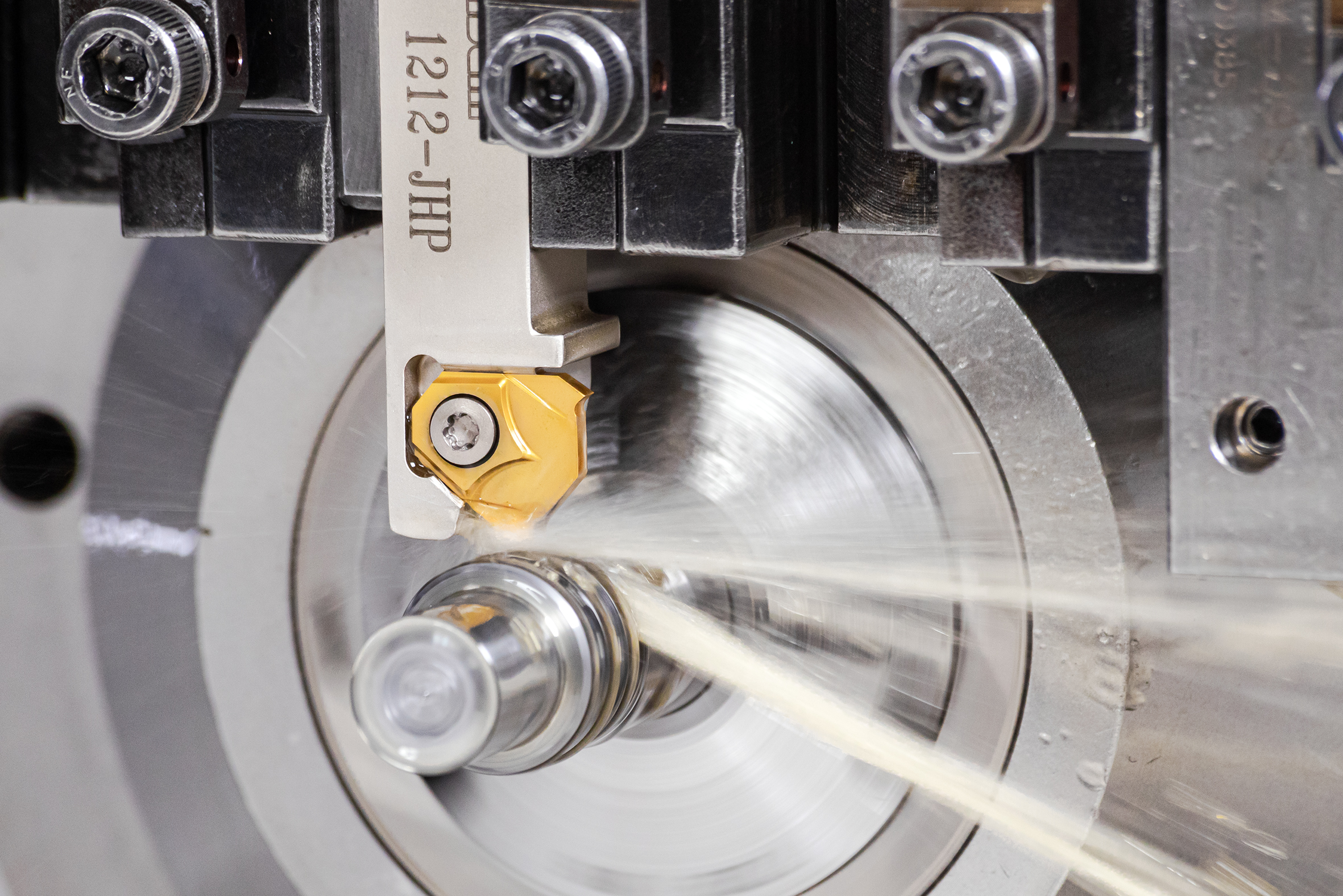